Contrôle en temps réel du transport interne à partir d'un jumeau numérique
- 4 avril 2025
- Communiqué de presse
- Entreposage et automatisation
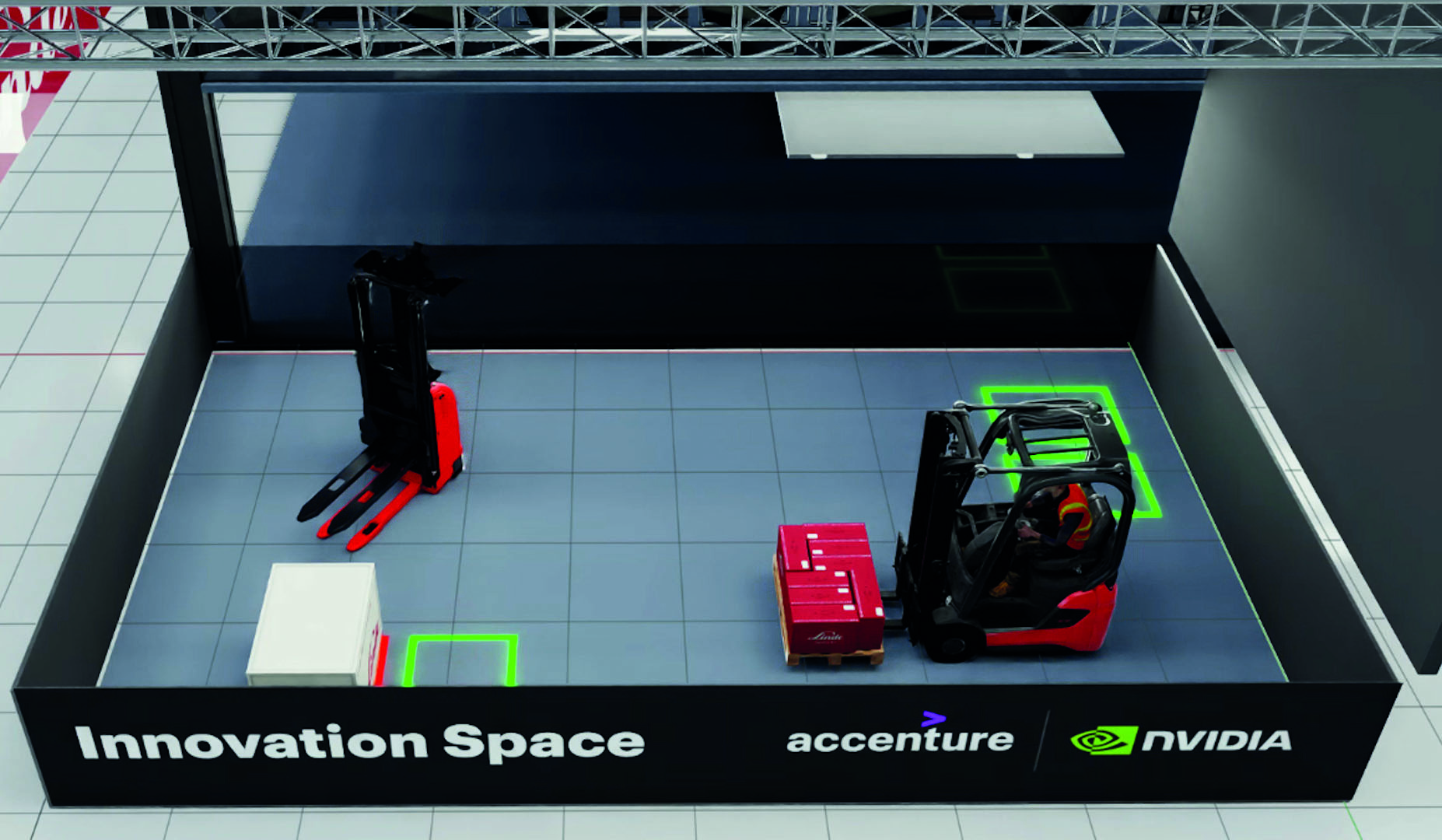
Apprentissage automatique et réseaux neuronaux
Du matériel et des logiciels intelligents, associés à une immense puissance de calcul, rendent chaque processus de l'entrepôt transparent. Les commandes peuvent également être traitées de manière plus rapide, plus fiable et plus souple grâce à la simulation continue. « L'apprentissage automatique et les réseaux neuronaux rendront l'entrepôt plus efficace. Le débit des marchandises augmentera, les flottes de machines manuelles et automatisées seront optimisées et le personnel sera utilisé plus efficacement. Tout cela permettra aux entreprises de réaliser d'importantes économies », déclare Ulrike Just, membre du directoire de Linde MH. « En tant que l'un des leaders en matière de technologie et d'innovation dans notre secteur, nous avons commencé à développer des solutions basées sur l'IA. Nous innovons pour améliorer la compétitivité de nos clients et préparer leurs flux de matériaux à l'avenir. Nous travaillons déjà sur des projets pilotes avec certains clients importants, puisque les investissements associés seront particulièrement rentables pour eux. »
Transparence totale grâce à une localisation en temps réel
La première étape de la stratégie de Linde MH consiste à mettre en réseau les chariots manuels. À cette fin, elle développe actuellement un système de localisation en temps réel qui fonctionne aussi bien à l'intérieur des entrepôts qu'à l'extérieur. Ce système utilise une technologie innovante à bande ultra-large pour déterminer l'emplacement de chaque chariot. Il indique ensuite aux caristes comment naviguer dans l'entrepôt ou les informe des nouveaux ordres de transport ou des ordres modifiés sur un écran. Le système combine les données de localisation avec les données du véhicule, telles que l'angle de braquage. De cette manière, l'itinéraire peut être ajusté en temps réel si, par exemple, il y a beaucoup de trafic sur l'itinéraire et que l'on perd trop de temps.
La deuxième étape consiste également à ajouter les chariots autonomes. Cependant, il faut une grande puissance de calcul pour les coordonner avec les chariots à commande manuelle et déterminer les itinéraires optimaux. « Si 100 véhicules ou plus doivent être coordonnés, cela n'est possible qu'avec une intelligence de haut niveau et un matériel capable de traiter de grandes quantités de données », explique Ron Winkler, directeur général de la Digital Business Unit chez Linde MH. « C'est là que l'IA de la plate-forme NVIDIA Omniverse entre en jeu. Elle permet de créer un jumeau numérique de l'entrepôt, une image virtuelle à l'échelle 1:1 de la réalité physique. » Dans cet environnement numérique, les simulations peuvent être calculées en quelques fractions de secondes. Qu'il s'agisse d'optimiser les itinéraires et la coordination des AMR et des chariots manuels, ou d'adapter l'agencement de l'entrepôt.
Pour ce faire, toutes les données physiques des chariots (puissance du moteur, angle de braquage, etc.) et de l'infrastructure (rayonnages, allées de circulation, etc.) sont stockées numériquement dans la plate-forme NVIDIA Omniverse. Cet espace virtuel est ensuite utilisé pour traiter toutes les informations provenant des capteurs, des caméras du véhicule et de l'infrastructure, des logiciels de gestion d'entrepôt et des systèmes de contrôle du véhicule.
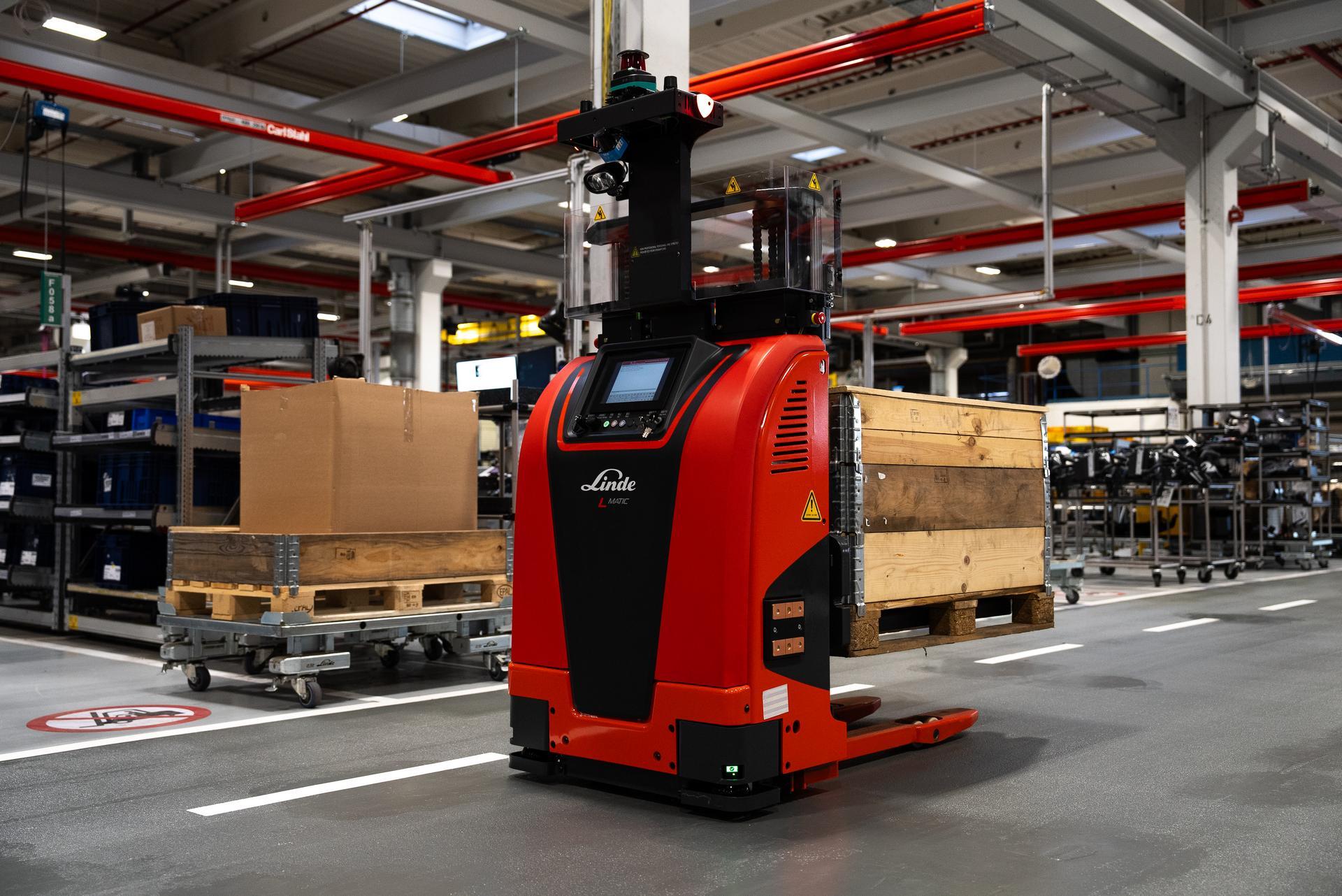
La simulation est clé
Les caméras installés sur les infrastructures et les chariots surveillent les zones de chargement et de stockage, et suivent les porteurs de charge ainsi que les AMR et les véhicules manuels. Ces images sont immédiatement interprétées et traitées par l'IA. Un exemple présenté au salon LogiMAT : un cariste apporte des marchandises dans la zone avant de l'entrepôt avec son chariot élévateur Linde. Depuis la zone de transfert définie, un gerbeur Linde autonome prend la palette et la transporte vers les rayonnages. Pour documenter et tracer de manière transparente le matériel et les marchandises sur la plateforme Omniverse, la caméra mobile du chariot élévateur télécharge automatiquement une photo de la charge lorsque la palette est prise. En même temps, la caméra reconnaît les personnes et les obstacles et adapte immédiatement le comportement du chariot élévateur à la situation. Les caméras fixes de l'entrepôt fournissent au système des informations sur l'occupation des zones de stockage et enregistrent également les éventuelles collisions avec des personnes. Cela permet aux véhicules de réduire leur vitesse si nécessaire.
Mais que se passe-t-il si le cariste ne place pas la palette dans la zone spécifiée avec la précision requise par l'AGV ? Le jumeau numérique sait, grâce aux caméras fixes, que la palette est positionnée et a transmis l'ordre de prélèvement au Linde L-MATIC core autonome. Cependant, grâce à la caméra intelligente de l'AGV, l'IA sait que la palette n'est pas correctement positionnée et cherche une solution. Une situation similaire se produit lorsque des caisses glissent ou qu'une partie de la charge dépasse. Dans ce cas, les caméras fixes le remarquent et l'IA conclut que les marchandises ne peuvent pas être prises en charge par un AGV. Le Linde L-MATIC core s'arrête alors et attend qu'une autre tâche de transport lui soit assignée. Simultanément, l'IA calcule quel véhicule manuel situé à proximité peut prendre en charge cette tâche de manière efficace.